Graphene Nanoribbons: Production & Applications
Ayrat M. Dimiev1, James M. Tour2
1EMD Performance Materials Corp., 70 Meister Ave, Somerville, NJ 08876 USA, 2Departments of Chemistry, Materials Science and NanoEngineering, and Computer Science, and the Smalley Institute for Nanoscale Science and Technology Rice University, MS-222, 6100 Main Street, Houston, Texas 77005 USA
Introduction
Graphene is a one-atomic-layer thick two-dimensional material made of carbon atoms arranged in a honeycomb structure. Its fascinating electrical, optical, and mechanical properties ignited enormous interdisciplinary interest from the physics, chemistry, and materials science fields.1–3 The newly discovered properties pave the way to applications in transparent conductive films, electronic and opto-electronic devices, actuators, sensors, composites, and more.
Graphene nanoribbons (GNRs) are narrow strips of graphene. The quasi one-dimensional nature of GNRs results in additional advantages over graphene sheets, the more widely known two-dimensional counterpart to GNRs. For example, the high aspect ratio of GNRs significantly lowers the percolation threshold in conductive films and polymer composites, and renders them suitable for spinning fiber from their liquid crystalline alignment.
Synthesis Methods
The structure and physical properties of GNRs vary significantly depending on the synthesis method—a single term for all GNRs can cause confusion among non-experts because of the resulting structural difference between different types of GNRs. Today, there are three major approaches for fabrication of GNRs: 1) cutting from graphene using lithography; 2) bottom-up synthesis from polycyclic molecules; and 3) unzipping of carbon nanotubes (CNTs). In fact, GNRs produced using those three methods are very different and have little in common.
Lithography
This approach yields single-layer GNRs on a substrate surface. The number of publications on this approach is significant. The use of lithographically produced GNRs is limited to applications where GNRs lie flat on a surface. Bulk quantities cannot be produced using lithographic methods. Also, due to inherent limits in the lateral resolution of lithography-based methods, lithographically produced GNRs have jagged edges.4–6 While this method produces highly precise and very narrow GNRs, the resulting uncontrolled jagged edges make it difficult to control the electronic properties of the resulting materials.
Bottom-Up
The bottom-up fabrication of GNRs involves multi-step organic synthesis based on cyclization of pre-synthesized polymer chains. This method allows for the creation of very narrow ribbons with atomically precise edge configuration.7–9 Until recently, this type of GNRs could only be prepared on the surface of a substrate,7,8 limiting the potential for bulk production. Despite the fact that such ribbons have been recently synthesized in a scale of hundreds of milligrams,9 it is difficult to see their actual applications in the near future. While the high precision and narrow size distribution resulting from the bottom-up synthesis of GNRs may yield future benefits, there are currently no ready-to-use techniques to further process these tiny structures. This technique has not yet been fully exploited, and it is difficult to envision its actual application in the near future.
Unzipping
The third approach to the fabrication of GNRs is based on the longitudinal opening, or unzipping, of multi-walled carbon nanotubes (MWCNTs).10,11 The reported techniques vary, but almost all of them are solution-based processes. The major advantage of this approach over the first two is the potential of mass production on the kilogram scale. Significantly lower cost is another advantage. Also, based on the number of recent publications, it is likely that these CNT-derived GNRs will be the first to find actual applications. Herein, we will review the various aspects of GNRs produced by unzipping of carbon nanotubes as well as their current and emerging applications.
Production of GNRs by Unzipping of Carbon Nanotubes
The Tour group first developed the method used to produce GNRs by longitudinal splitting of carbon nanotubes using potassium (K) vapor and then later in solution using sodium-potassium alloy (Na/K)10 (Figure 1).
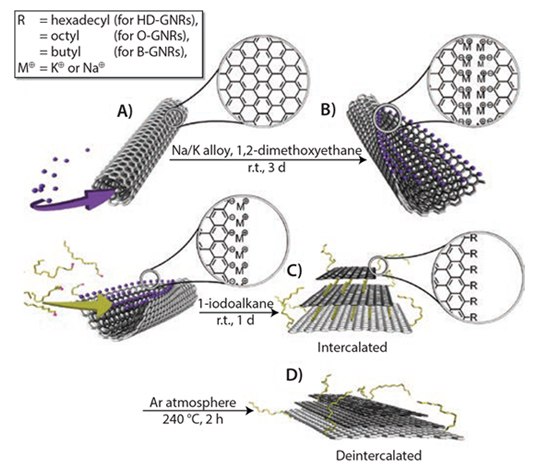
Figure 1.Scheme for unzipping and functionalization of GNRs: (A) intercalation of potassium between the walls of MWCNTs; (B) splitting process of MWCNTs and formation of GNRs with active carboanionic edges (M = K or Na); (C) in situ functionalization and intercalation of GNRs with alkyl groups; and (D) deintercalation of functionalized GNRs. Reprinted with permission from ACS Nano, 2012, 6, 4231–4240. Copyright 2012 American Chemical Society.
MWCNTs are unzipped via intercalation of the K/Na alloy between the nanotube walls in a 1,2-dimethoxyethane (DME) solvent as shown in Figure 1A. This lattice expansion induces sufficient stress to longitudinally break the nanotube walls. The carbon atoms at the newly formed edges are reduced to their highly reactive carboanionic form (Figure 1B), making them highly susceptible to electrophilic attack. If the intermediate product (Figure 1B) is quenched with methanol, followed by aqueous washing, the metal cations on the edges are replaced with protons.This yields H-terminated GNRs (Prod. No. 797774) or simply GNRs. Figure 2 shows MWCNTs fully unzipped after treatment. These GNRs, however, are not completely flat due to van der Waals interaction between the nanotube walls. The GNRs can be completely flattened and partially exfoliated by bath sonication in chlorosulfonic acid.11 The electrical conductivity of the flattened 3.5 to 5 nm thick GNR stacks, comprising 10 to 14 layers, is in the range of 70,000 to 95,000 S/m.11 These values are comparable to the data reported for other graphitic structures.
To prepare alkylated GNRs (alk-GNRs) (HD-GNRs when R=hexadecyl, Prod. No. 797766), the intermediate product is exposed to 1-halo-alkanes (Figure 1C). Intercalated potassium is successfully replaced by haloalkanes that predominantly functionalize the edges (and, to some extent, the basal planes) and serve as intercalents in the resulting alk-GNRs. The alk-GNRs bearing long alkyl chains are well-dispersible in organic solvents such as alcohols, ketones, ethers, and alkanes (Figure 3). Particularly stable dispersions are produced in chloroform or chlorobenzene.

Figure 2.SEM images of (A) and (B) MWCNTs and (C) and (D) fully unzipped MWCNTs.
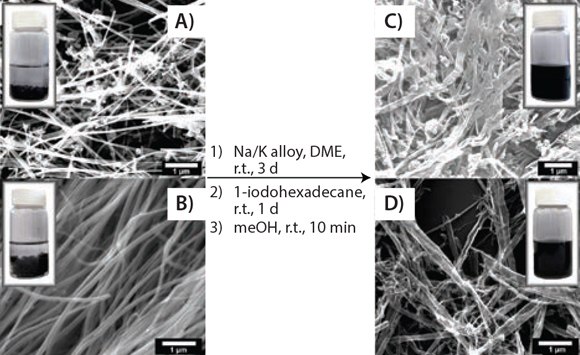
Figure 3.Solubility test. SEM images showing the splitting and functionalizing of commercially available MWCNTs and the photographic difference in solubility between functionalized GNRs and pristine MWCNTs: (A) and (B) two different types of pristine MWNTs and a 0.1 mg/mL suspension in chloroform; (C) and (D) hexadecylated (HD)-GNRs and a 0.1 mg/mL stable dispersion in chloroform. Reprinted with permission from ACS Nano, 2012, 6, 4231–4240. Copyright 2012 American Chemical Society.
Raman spectroscopy (Figure 4) has proven an effective and nondestructive method for the characterization of graphitic carbon nanostructures. The main Raman signals in the spectra of any type of graphitic carbon are the G-band at ~1,680 cm-1 and the 2D-band at ~2,700 cm-1. The D-band at ~1,360 cm-1 is caused by defects serving as photon scattering centers, and it is indicative of the quality of the graphitic structure. Thus, evolution of the D-band during unzipping and functionalization procedures gives valuable information about the nature of as-prepared GNRs. The Raman spectrum of MWCNTs contains only weak D-band signals, suggesting high crystallinity of the parent MWCNTs. In the spectrum of as-produced protonated GNRs, the D-band intensity significantly increases. This is attributed to the carbon atoms on ribbon edges, which act as photon scattering centers. After alkylation, the D-band intensity increases even further, indicating increase in the defect density. We attribute this observation to some covalent functionalization of the GNRs’ basal planes. Basal plane alkylation converts the sp2 carbon atom to the sp3 carbon atom, thus creating a defect in the otherwise perfect graphene plane. The G/2D ratio for alk-GNRs corresponds to that of a single layer graphene. This suggests separation of GNRs caused by intercalation of alkyl chains between the GNRs.
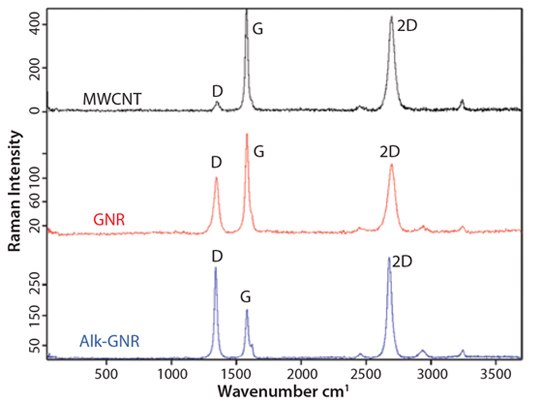
Figure 4.Raman spectra for MWCNTs, GNRs and alk-GNRs.
Potential Applications of GNRs
Both H-terminated GNRs (Prod. No. 797774) and alkylated GNRs (Prod. No. 797766) have a broad range of potential applications. The most apparent is the incorporation of GNRs in polymer hosts for the fabrication of novel composite materials. GNRs have the same high aspect ratio as their parent MWCNTs, but differences in their nanostructure produce unique and unexpected results. For example, the incorporation of GNRs into a dielectric polymer host dramatically changes its electric properties12,13 in a way that is significantly different from that achieved by incorporation of MWCNTs. The most intriguing result is that GNRcontaining polymer composites possess remarkably low loss (<0.02) at reasonably high permittivity values (Figure 5). This is important because the miniaturization of electronic components requires materials with high permittivity and low loss in the radio and low microwave frequency region. In the high frequency microwave region, low loss is critical for antennas and other military applications. By varying the type and content of GNRs, the loss and permittivity of composites can be tuned to desirable values over a wide range. The dielectric constant can be tuned from moderate to extremely high (>1,000) values, while the corresponding loss tangent can be varied from ultralow (<0.02) to high (~1.0).13
Another promising application of GNRs is as electrode material for batteries and supercapacitors. In one reference,14 a unique hierarchical structure composite of graphene-wrapped MnO2-GNRs (GMG) was successfully designed and synthesized (Figures 6 and 7). In this composite, graphene flakes tightly sandwiched nanosized MnO2 that grew directly on the GNRs.
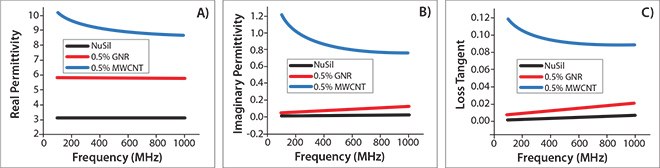
Figure 5.Dielectric properties of the GNR/NuSil (silicon elastomer) composites. (A) Real permittivity, (B) imaginary permittivity, and (C) loss tangent of pure NuSil (black), MWCNT/NuSil (blue), and GNR/NuSil (red) composites containing 0.5 wt % incorporated conductive filler. Reprinted with permission from ACS Appl. Mat. Interf. 3, 4657-4661 (2011). Copyright 2011 American Chemical Society.
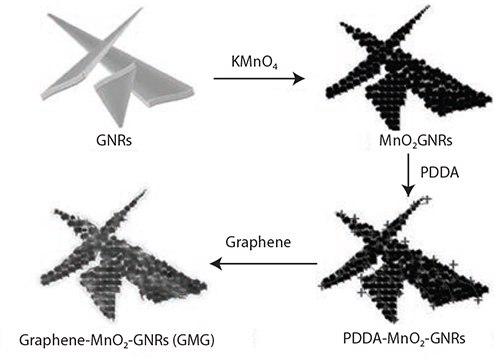
Figure 6.Illustration of the synthesis of the graphene-wrapped MnO2-GNRs (GMG) composite. Reprinted with permission from Adv. Mater. 2013, 25, 6298–6302. Copyright 2013 John Wiley and Sons.
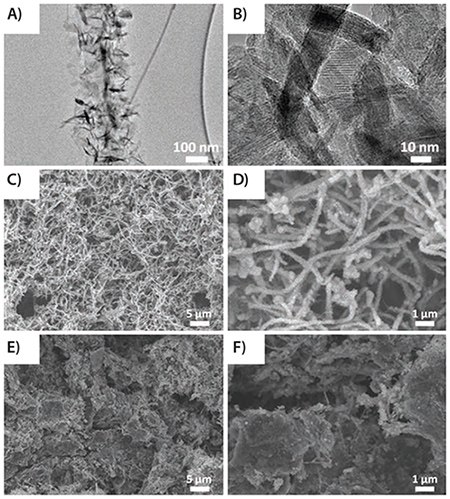
Figure 7.(A) and (B) TEM images of MnO2-GNRs (MG); (C) and (D) SEM images of MG; and (E) and (F) GMG. Reprinted with permission from Adv. Mater. 2013, 25, 6298–6302. Copyright 2013 John Wiley and Sons.
The synthesis of the GMG composite has produced an effective component to improve the electrochemical stability of the electrode materials for lithium-ion batteries.
Electrochemical experiments demonstrate that the GMG exhibits enhanced specific capacity and improved cycling stability as anode materials compared to MnO2-graphene or pure MnO2 because of the synergic effect between the graphene, GNRs, and MnO2. These characteristics helped achieve stable capacity at several different current densities. For example, the value of specific capacity increased to 890 mAh/g at 180 cycles from 672 mAh/g at 2 cycles in the current density of 0.1 A/g. The rate performance demonstrates that the GMG electrode remained stable after extended rate cycles. For GMG, in the first 5 cycles, the specific capacity decreased as had been seen with MG. After 5 cycles, the value of GMG discharge capacity decreased from 571 mAh/g at 6 cycles to 465 mAh/g at 20 cycles, but then increased to 648 mAh/g at 170 cycles. Even after 250 cycles, the GMG still maintained a specific capacity of 612 mAh/g. Moreover, the Coulombic efficiency of GMG was maintained at over 99%, excluding the first several cycles.
In another work,15 GNRs were used to fabricate a nanocomposite material of polyaniline (PANI) and GNRs (Figure 8). GNRs were selected as a template on which PANI nanorods were grown. A nanocomposite of PANI-GNRs was prepared by the in situ polymerization of aniline in the presence of GNRs. In this composite, GNRs not only serve as the substrate to grow the PANI nanorods and improve the electrical conductivity of the composite, but also increase the effective utilization of PANI and enhance the mechanical property of the composite.
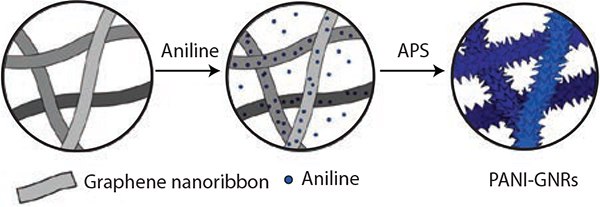
Figure 8.Illustration of the synthesis of the PANI-GNRs composite with PANI polymerized directly on the GNRs using APS (ammonium persulfate). Reprinted with permission from ACS Appl. Mat. Interf. 2013, 5, 6622–6627. Copyright 2013 American Chemical Society.
The resulting composite has a high specific capacitance of 340 F/g and stable cycling performance with 90% capacitance retention over 4,200 cycles. The high performance of the composite results from the synergistic combination of electrically conductive GNRs and highly capacitive PANI.
As another potential application, alk-GNRs were used in polymer composites to lower the permeability of gases.16 A thermoplastic polyurethane (TPU) composite film containing alk-GNRs was produced by solution casting. The HD-GNRs (Prod. No. 797766) were welldistributed within the polyurethane matrix, leading to phase separation of the TPU. Nitrogen gas effective diffusivity of TPU was decreased by three orders of magnitude with only 0.5 wt % alk-GNRs (Figure 9).
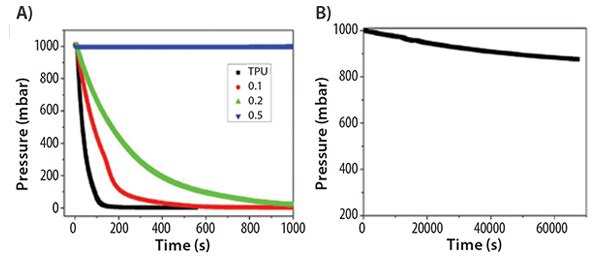
Figure 9.(A) Pressure drop of TPU and TPU/HD-GNRs films with respect to time. (B) Pressure drop of TPU/0.5 wt % HD-GNRs composite film over a longer time period. Reprinted with permission from ACS Appl. Mat. Interf. 2013, 7, 10380–10386. Copyright 2013 American Chemical Society.
The incorporation of alk-GNRs also improved the mechanical properties of the composite films, as predicted by the phase separation and indicated by tensile tests and dynamic mechanical analyses. The improved properties of the composite film could lead to potential applications in food packaging and lightweight mobile gas storage containers. As a demonstration for their potential to inhibit gas permeation in Figure 9, see the comparison of efficacies in Table 1.
Barrier Material | Gas Permeation |
---|---|
GO17 (Prod. No. 763705, etc) | 80× decrease at 3 wt % filler |
Nanoclay18 (Prod. No. 682608, etc.) | 14× decrease at 28 wt % filler |
HD-GNRs (Prod. No. 797766) | 1,000× decrease at 0.5 wt % filler |
Conclusion
Both GNRs and alk-GNRs have great potential for numerous applications. Currently, the most promising applications are polymer composites and electrode materials for energy storage. It is expected that these diminutive structures will garner increased interest as they become more readily available for researchers and their unique properties become more thoroughly understood.
References
如要继续阅读,请登录或创建帐户。
暂无帐户?