Single-Use Bioprocessing Film Selection
Single-use technologies are used throughout bioprocessing to improve process flexibility and efficiency and mitigate the risk of product and process contamination. Bioprocessing films are a key component of any single-use technology and, before implementing, the end-user should confirm the characteristics of the film meet the requirements of the bioprocessing operation and the film is compatible with their process fluid. Single-use bioprocessing operations vary widely in scale, complexity, and level of risk: a small bag for sample collection will have different requirements to a 2000 L bioreactor bag which will be different to a header bag in a final fill operation.
Understanding the specific process requirements will guide risk assessment and enable collection of appropriate product data. A key consideration for implementation of any single-use technology is container robustness. Most biomanufacturers dedicate considerable resources on inspecting single-use technologies before they are approved for use in manufacturing and many buy extra bags to account for those rejected during inspection. Container leaks at any scale are inconvenient, but for large volume applications in particular, film robustness is critical as leaks and compromised seals can result in costly disruptions in the manufacturing environment.
Our portfolio of single-use containers for bioprocessing are made with either Ultimus® or PureFlex™ films. Containers made with Ultimus® Film are designed for more challenging single-use applications such as mid to large-volume liquid processing applications including storage, transportation, and process intermediate fluid transfer where enhanced bag strength, improved durability and leak resistance is needed.
Containers made with PureFlex™ film can be used throughout manufacturing for low-volume, less critical liquid processing applications. Bags made with PureFlex™ film enable biomanufacturers to scale their process with a single fluid-contact material.
The purpose of this technical article is to provide information on our bioprocessing films to support you in making informed decisions for your process needs.
- Characteristics of Ultimus® Film
- Characteristics of PureFlex™ Film
- Comparing specifications of Ultimus® & PureFlex™ films
- Film recommendations for different applications
- Qualifying and implementing single-use systems in your process
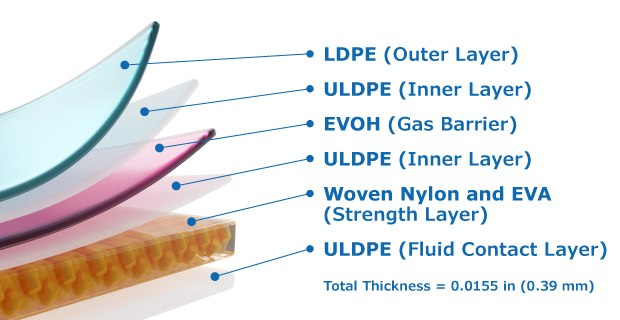
Ultimus® film was designed to meet the needs of the toughest and highest value single-use applications including large-volume liquid processing and fluid transportation, where extreme durability is needed. Ultimus® Film is available in Mobius® 3D process containers, Mobius® iFlex Bioreactors, Mobius® Power MIX, and Mobius® MIX assemblies.
Our Ultimus® film technology provides enhanced bag strength, improved durability and leak resistance through a novel strength layer reinforced by woven nylon, Figure 1. The fluid contact layer is made up of ultra-low density polyethylene (ULDPE), is free of Irgafos® 168, has a low extractable profile, and supports healthy cell growth. The gas barrier layer is made of ethylene vinyl alcohol copolymer (EVOH). The outer layer of clean low-density polyethylene (LDPE) increases film resistance to leak formation through abrasion, puncture, stretching, and tearing. The woven nylon strength layer is strategically placed between layers of ethylene vinyl acetate (EVA), and significantly increases the overall durability of the film.
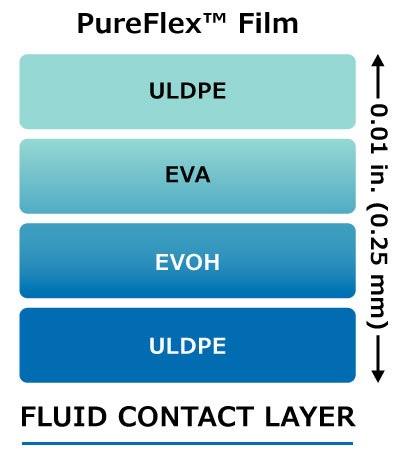
Figure 2. Structure of Pureflex™ film
PureFlex™ film is extremely flexible and can be used for low volume liquid volume applications anywhere in the drug manufacturing process. Manufacturers using PureFlex™ film can scale their process with a single fluid-contact material, thus simplifying the single-use qualification process.
PureFlex™ film contain an ultra-low-density polyethylene (ULDPE) inert fluid contact layer, a low permeability gas barrier layer made of polyethylene vinyl alcohol copolymers (EVOH) and ethylene vinyl acetate (EVA) layers to maintain flexibility, Figure 2.
Properties | Tests | Ultimus™ Film Average Values | PureFlex™ Film Average Values1 |
Abrasion Resistance at 500 g | ASTM® F3300 - 18 | 4007 strokes |
|
Puncture Resistance | ASTM® F-1306 - 16 | 31.3 lbf (139.23N) |
|
Flex Durability | ASTM® F-392 | No holes at 900 cycles |
|
Tensile Strength at Break (psi) | ASTM® D882 | 5200 psi (35.9MPa) | 2700 psi (18.6 Mpa) |
Elongation2 | ASTM® D882 | Test not applicable due to the reinforced structure | 570 % |
Yield Strength2 | ASTM® D882 | Refer to tensile strength at break. | 1360 psi (9.4 Mpa) |
Modulus (Young’s) | ASTM® D882 | 31.1 kpsi (214.4 Mpa) |
|
Toughness2 | ASTM® D882 | Test not applicable due to the reinforced structure. | 9100 in.-lbf/in.3 (63 M J/m3) |
Seam Strength | ASTM® D882 | 57.2 lbf/in (100N:cm) | 18 lbf/in. (32 N/cm) |
O2 Transmission Rate | ASTM® F1307 at 23 °C | 0.009 cc/100 in. /24 h (0.14 cc/m2/24 h) | 0.063 cc/100 in. /24 h (0.98 cc/m2/24 h) |
CO2 Transmission Rate | ASTM® F2476 at 23 °C | <0.065 cc/100 in.2/24 h (1.01 cc/m2/24 h) | 0.13 cc/100 in. /24 h (92 g/m2/24 h) |
Moisture Vapor Transmission Rate (MVTR) | ASTM® F1249 at 23 °C | 0.036 g/100 in.2/24 h (0.558 g/m2/24 h) | 0.034 g/100 in. /24 h (0.53 g/m2/24 h) |
Haze | ASTM® D1003 | 50% | 23% |
Glass Transition Temperature2 | ASTM® D5026 | Measurement is not meaningful due to composite structure. | -26 °C |
Film Thickness | ASTM® D374 | 0.0155 in. (0.39 mm) | 0.01 in. (0.25 mm) |
Operating Temperature Range3 |
| 2 - 60 °C | -80 – 60 °C |
Properties | Tests | Ultimus® Film | PureFlex™ Film1 |
Biological reactivity | USP<88> | Film materials meet the criteria for Biological Reactivity Testing. These tests can be any or a combination of the following test methods: USP<88> Class VI (in vivo), USP<87> (in vitro), ISO 10993-5 (in vitro). | Meets requirements
|
Cytotoxicity | USP<87> | Film materials meet the criteria for Biological Reactivity Testing. These tests can be any or a combination of the following test methods: USP<88> Class VI (in vivo), USP<87> (in vitro), ISO 10993-5 (in vitro). | Meets requirements
|
Bacterial Endotoxin | USP<85> | Film materials meet the criteria for Biological Reactivity Testing. These tests can be any or a combination of the following test methods: USP<88> Class VI (in vivo), USP<87> (in vitro), ISO 10993-5 (in vitro). | Meets requirements
|
Physiochemical Test for Plastics Heavy Metals Buffering Capacity Non-volatile Residuals Residue on Ignition | USP<661 | Film materials meet the criteria for Biological Reactivity Testing. These tests can be any or a combination of the following test methods: USP<88> Class VI (in vivo), USP<87> (in vitro), ISO 10993-5 (in vitro). |
Meets requirements Meets requirements Meets requirements Meets requirements |
Aqueous Solutions for Parenteral Injections Appearance Acidity & alkalinity Reducing Substrate Transparency, Absorbency | Per Ph. Eur. 3.2.2.1
|
Meets requirements
|
Meets requirements
|
Particulate Matter | USP<788> | Meets requirements | Meets requirements |
Hemolysis | ISO 10993-4 | Meets requirements | Meets requirements |
Film recommendations for different applications
For any high value application, irrespective of volume, the superior strength, robustness, and leak resistance of Ultimus® film makes it the preferred film for single-use processing. Such applications could include mixing, storage, and transportation of process intermediates or drug substance.
For lower value applications involving buffer or cell culture media, at volumes over 100 L scale, we recommend bags and containers made with Ultimus® film to minimize risks from leaks. When volumes are less than 100 L, bags and containers made with time-tested PureFlex™ film will deliver the performance needed and enable easy scalability, Figure 3.
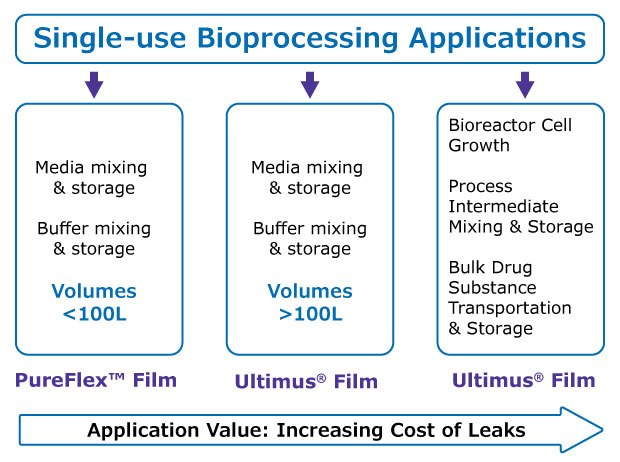
Our single-use assembly and mixer bag offerings made of Ultimus® and Pureflex™ films are listed in Table 3.
| 2D Assemblies | Drum Assemblies | Collapsible Bin Assemblies | Stainless Steel Assemblies | Transport Bin Assemblies |
Scales | 50, 100 mL 1, 5, 10, 20, 50 L | 50, 100, 200, 500* L | 100, 200*, 250, 500, 1000 L | 100, 250, 500*, 1000*, 2000 L | 200, 500, 1000* L |
PureFlex™ film Standard | ✔ | ✔* |
|
|
|
PureFlex™ film Configurable | ✔ | ✔ | ✔ | ✔ | ✔* |
Ultimus® film Standard |
|
| ✔* | ✔* |
|
Ultimus® film Configurable |
|
| ✔ | ✔ | ✔ |
| Mobius® MIX carriers with standard control box | Mobius® MIX carriers with Ready To Connect control box | Mobius® MIX carriers with Ready To Connect control box | Mobius® Power MIX carriers (standard control and Ready To Connect control box) | Mobius® Power MIX carriers (standard control and Ready To Connect control box) |
Scales | 10, 50, 100, 200, 500, 1000 L | 100, 200, 500 L | 1000 L | 100, 200, 500 L | 1000, 2000, 2500, 3000 L |
PureFlex™ film Standard | ✔ | ✔ | ✔ | ✔ | ✔ |
Configurable | ✔ | ✔ | ✔ | ✔ | ✔ |
Ultimus® film Standard |
| ✔ |
| ✔ |
|
Configurable |
| ✔ |
| ✔ |
|
Qualifying and implementing single-use systems in your process
Implementing single-use technologies into a bioprocessing workflow requires close interactions between the biomanufacturer and single-use supplier for both technology selection and ensuring the technology is suitable for the intended application. Information collected from the single use technology supplier is typically utilized by the biomanufacturer for their own process-specific risk assessment.
Successful implementation relies on suppliers qualifying single-use assemblies against industry expectations for numerous quality specifications related to particulates, endotoxin, bioburden, extractables and leachables, sterilization, shelf life, packaging and transport, and integrity testing. While drug manufacturers, may not be directly responsible for all the testing, it is expected that they audit their suppliers and have confidence in their supplier’s manufacturing process, equipment and in-process and release testing practices.
To maintain integrity of the single use technology after leaving the supplier’s facility, manufacturers should have well documented procedures, that align with supplier best practices, on how to receive, inspect, store, unpack, prepare and use the single-use technology, Figure 4.
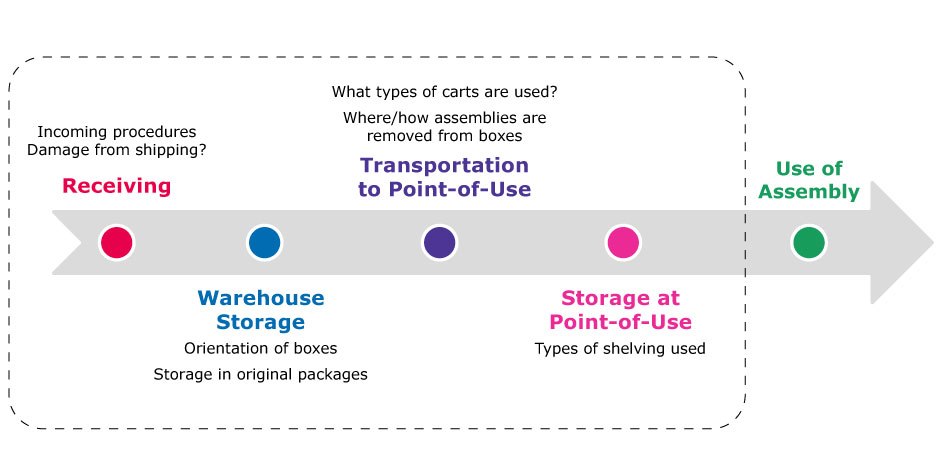
For selecting, testing and validating your filters, assemblies, and single-use systems for drug manufacturing and processing our Single-Use and Filter Validation Services team can help you develop and implement a validation strategy to meet regulatory expectations.
The Emprove® Program provides the documentation needed for implementation of single use systems in biomanufacturing. The detailed product information in the Emprove® Dossiers enables more agile, risk-based decisions, minimizing time and investment from biomanufacturers. The Emprove® Program includes single use components, filters, connectors, and film, as well as a wide range of other products used in bioprocessing such as chromatography resins, cell culture media and chemicals. Description for the dossier contents related to single-use technologies are below:
- The Emprove® Material Qualification Dossiers (MQD) include product test specifications, release criteria, and regulatory information for the components as well as materials used for component qualification.
- The Emprove® Quality Management Dossiers (QMD) includes quality and validation information including site qualification, irradiation sterilization process and packaging validations and site qualification.
- The Emprove® Operational Excellence Dossier (OED) includes extractables data following BioPhorum and USP <665> guidance to support patient safety evaluation.
- The Emprove® Component Extractable Reports includes extractables data following USP <665> guidance to support patient safety evaluation. The reports are for single-use components made by third-party suppliers.
- The Emprove® Advanced Qualification Dossier (AQD) supports custom and configurable assemblies and includes:
- All available component qualification information and extensive USP <665> extractables data for all the components in the assembly.
- Information on extractables, bills of material, regulatory statements, component surface area information, original manufacturer information, shelf-life statements, and customer-approved drawings of the assemblies.
- Data needed by end users to conduct risk assessments and patient safety evaluations of their assemblies
References
如要继续阅读,请登录或创建帐户。
暂无帐户?