Promote Optimal Cell Growth with Single-Use Bioprocessing Film
Single-use technologies are increasingly being used in biomanufacturing to achieve greater efficiency and productivity, reduce capital investment, and minimize cross-contamination. However, bioprocessing containers are composed of multilayered plastics and component polymers with properties that can be influenced by bioprocessing requirements such as sterilization by irradiation.
Dependent on the film and process conditions, these plastics and polymers increase the risk of elevated levels of extractables and leachables (E & L) in the process fluid which must be controlled to avoid patient safety concerns.1
Other single-use bioprocessing container components, including Irgafos® 168, are antioxidants that provide stability and integrity to polymers during production and use. But the presence of Irgafos® 168 in single-use bioprocessing containers can impact the productivity of upstream applications.
Read more about
What is Irgafos® 168 and why should you be concerned?
Irgafos® 168 (tris(2,4‐di‐tert‐butylphenyl)phosphite) is an antioxidant commonly used in the production of single-use films for bioprocessing.2 Following sterilization by gamma irradiation, Irgafos® 168 releases the by-product bis (2,4-di-tert-butylphenyl) phosphate (bDtBPP), a compound known to adversely impact growth of Chinese Hamster Ovary (CHO) cells, even at low concentrations.3 The presence of bDtBPP in sterilized single-use bioprocessing containers used for cell culture applications could limit cell growth and productivity. To mitigate this effect, Ultimus® film was developed with a fluid contact layer free of Irgafos® 168. In addition, this film is free of animal origin (AO) components and provides the robustness and leak resistance required for several bioprocessing applications, such as single-use bioreactor bags.
Irgafos® 168-free film promotes optimal cell growth and viability
Studies benchmarked performance of a panel of CHO cell lines grown in cell culture media that had been stored in bags made with Ultimus® film, against media stored in glass bottles. Before use, all bags were gamma irradiated at 25-40 kGy and glass bottles were sterilized by autoclaving.
Batch cultures
For seven batch cultures, the integrated viable cell density (IVCD) and cell viability were not statistically different when grown in media stored in Ultimus® bags or glass bottles when compared to a negative control bags containing Irgafos® 168. Figure 1 shows the results for one selected cell line.
A. Viability for Batch Culture
Cell Line 3
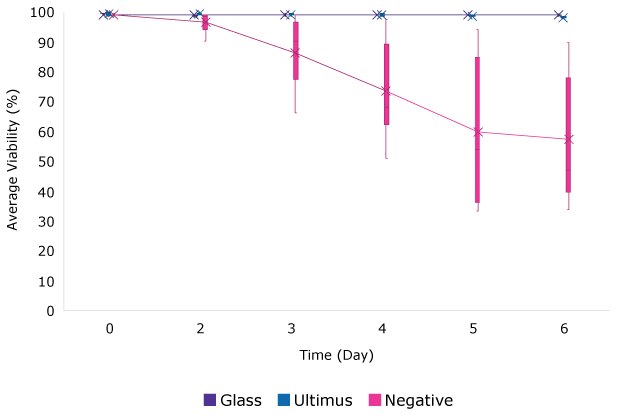
B. IVCD for Batch Culture
Cell Line 3
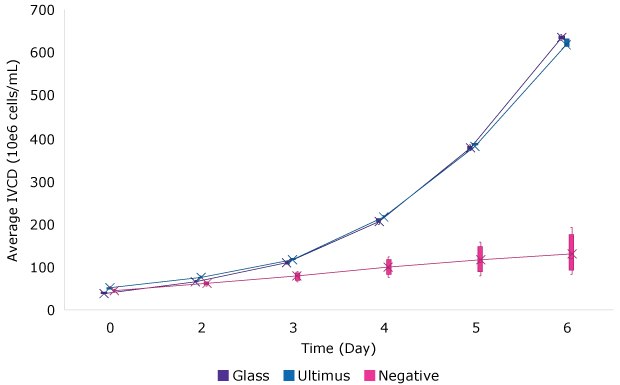
Figure 1.Viability (A) and IVCD (B) for batch culture of a CHO cell line grown in media stored in bags made from Ultimus® film, glass, or a commercially available film containing Irgafos® 168. Each data point represents the mean (and standard deviation) of 6 replicates.
Fed batch cultures:
IVCD, cell viability and protein titer from fed batch cultures of CHO cell line 3 grown in media stored in Ultimus® bags or glass bottles are shown in Figure 2. As with the batch cultures, no differences in fed batch cell culture performance were identified between the media stored in Ultimus® film and glass bottles.
A. Viability for Fed Batch Culture
Cell Line 3
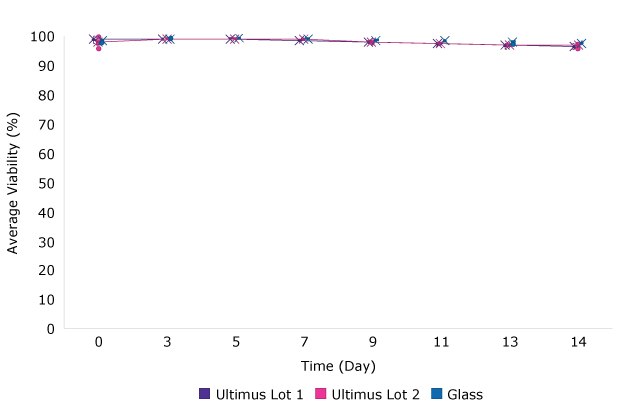
B. IVCD for Fed Batch Culture
Cell Line 3
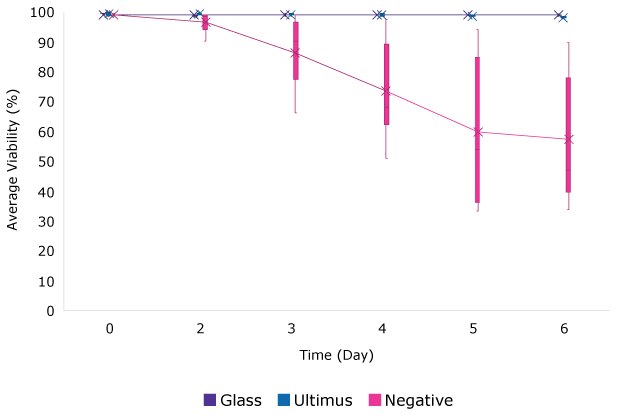
C. Titer for Fed Batch Culture
Cell Line 3
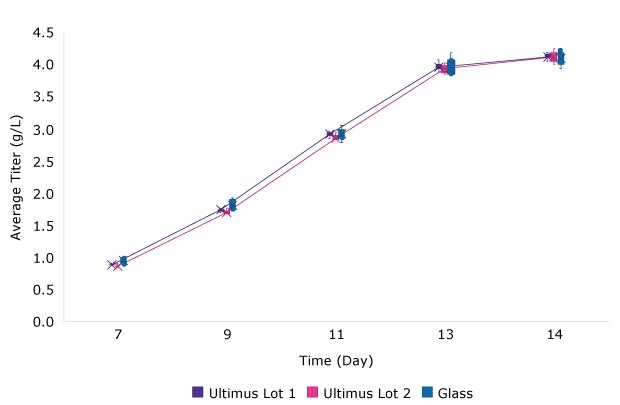
Figure 2.Viability (A) and IVCD (B) and Titer (C) for batch culture of a CHO cell line over 14 days when grown in media stored in glass or bags made from Ultimus® film. Each data point represents the mean (and standard deviation) of at least 9 replicates.
Single-use bioprocessing film and product quality attributes
The antibody produced by the selected cell line was evaluated to determine if the storage conditions of cell culture media altered the product quality.
Figure 3 shows the results of charge (A) and aggregate profile (B) analysis of the secreted antibody. Profiles were similar between all samples collected, confirming that media storage in Ultimus® bags did not negatively impact product quality attributes.
Charge Profile
Charge Analysis
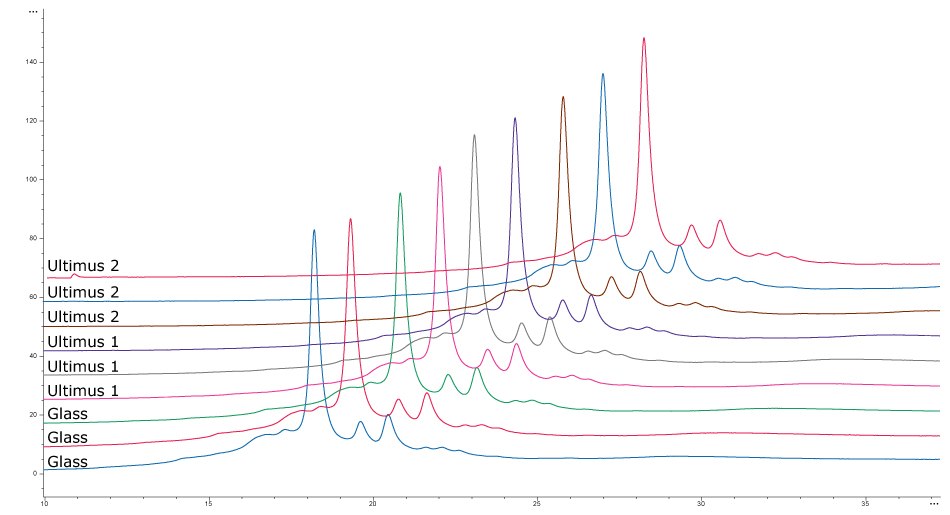
Aggregation Profile
Size Exclusion Chromatography

Figure 3.Comparison of charge (A) and aggregate profile (B) of secreted antibody grown in fed-batch cultures with media incubated in different lots of Ultimus® film or glass.
Bioprocessing Film Free of Animal Origin Components and Irgafos® 168 Minimizes Risks
These studies with CHO cells expressing either an antibody or recombinant protein, confirm Ultimus® film promotes equivalent cell growth and productivity to glass containers.
The Irgafos® 168-free fluid contact layer, and absence of animal origin components throughout all layers of Ultimus® film results bioprocessing containers that minimize the risk of contamination while enabling optimal cell growth and productivity.
References
To continue reading please sign in or create an account.
Don't Have An Account?