Bioprocessing Bag Films: Key Characteristics & Properties
Single-use bags and containers are used throughout bioprocessing: from cell growth in single-use bioreactors, to buffer and media mixing and storage, to transportation of bulk drug substance. Bag selection is highly dependent on the application, processing scale and film composition. Single-use bioprocessing bags should be compatible with the fluid stream, sterilization by irradiation, have low extractables and leachables, and sufficient durability for the intended use.
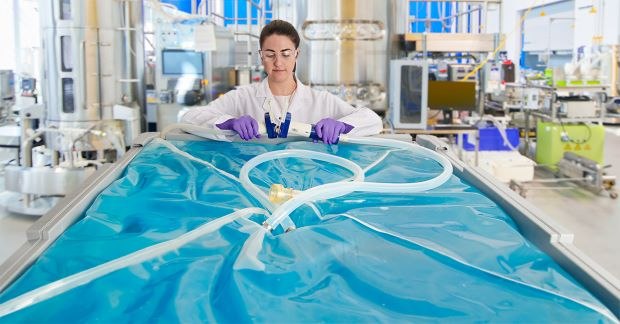
The Structure of Bioprocessing Film
Although some single-use bags contain a single-layer film, most bioprocessing bags are composed of multiple film layers:
- Outer layer: provides durability and resists abrasions, punctures, stretching and tearing which could cause leaks.
- Gas barrier and strength layers: sandwiched between the outer and fluid contact layers, these layers minimize oxygen and carbon dioxide transmission through the film while providing flexibility to minimize cracks and leaks.
- Fluid contact inner layer: on the bag interior is in direct product contact. This layer should not impact cell growth and performance and have a low extractable and leachable profile.
Considerations for Choosing Bioprocessing Film
To confirm the bioprocessing film provides the durability, strength and robustness needed for biomanufacturing, suppliers rely on tests conducted using benchmark American Society for Testing and Materials (ASTM) standards. High durability reduces leaks in single-use bags and minimizes costs for manufacturers.
Extractables and Leachables
Extractables and leachables (E & L) from the fluid contact layer of single-use film can adversely affect cell growth, product yield and quality. Before implementing single-use components in bioprocessing, it is recommended that manufacturers adopt quality risk management practices to confirm suitability of the components with their process conditions.1,2 Some suppliers offer E & L information on their components and additional services to help manufacturers assess E & L risk to their process.
Chemical, Irradiation and Biocompatibility
Chemical interactions can occur between the polymers in single-use bags and the process fluid and before implementing any single-use technology, it is important to consider chemical compatibility.3 Single-use film suppliers can help manufacturers to assess the level of product binding to single-use components by offering analytical assay services.
Before use, single-use bioprocessing containers are typically sterilized with gamma or X-Ray irradiation and it is critical that neither physical nor chemical container properties are adversely affected by irradiation.
The fluid contact layer of many single-use films contain the anti-oxidant, Irgafos® 168, and following gamma irradiation, the by-product bis (2,4-ditert-butylphenyl) phosphate (bDtBPP) is created. This by-product inhibits growth of Chinese Hamster Ovary (CHO) cells, the production cells for many monoclonal antibody and recombinant protein processes.4 A bioprocessing film that does not contain Irgafos® 168 has recently been developed and should be the preferred option for cell culture applications.
Gas Transfer and Animal Origin Components
Single-use bioprocessing bags and containers contain a gas barrier layer to maintain acceptable levels of oxygen and carbon dioxide within the bag while providing flexibility.
While the components of single-use bags are not derived from animals, manufacturers may add animal-derived components to improve film properties. However, such animal origin components may increase the risk of contaminating the process from pathogens of animal origin. Using films that don’t contain animal origin components such as PureFlex™ Film and Ultimus® Film, can minimize risk for manufacturers.
Film Durability (Flexibility, and Puncture and Tear and Abrasion Resistance)
The durability of single-use bags depends on the film’s flexibility, puncture, tear, and abrasion resistance and relies on the properties of multiple film layers. Improving durability of bioprocessing film, particularly for processes that use larger volume bioprocessing bags, minimizes the likelihood of leaks resulting costs for manufacturers.
Each bioprocessing film has a characteristic profile of materials, thickness, density, and other properties. The outer film layer resists abrasion and punctures from transportation and contact with other objects but the polyethylene vinyl polymers in the gas barrier layer can impact film flexibility. Ultimus® film contains a specialty grade of polymer which offers enhanced flexibility while limiting gas transmission. Importantly, the innovative woven nylon integrated in Ultimus® film structure delivers exceptional strength for the toughest bioprocessing applications, Figure 1.
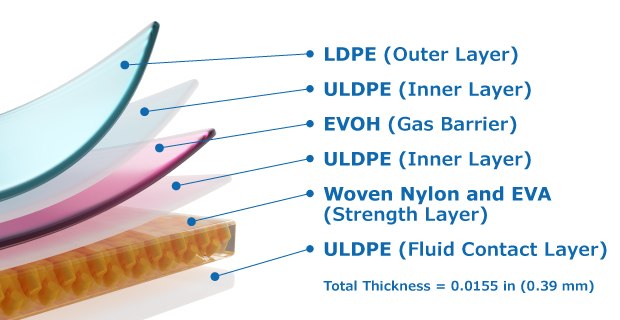
Figure 1:Ultimus® film structure
Cost benefits of Increased Bag Durability
Advances have been made in film and bag design, however, leaking of single-use bags remains a challenge to widespread implementation. To mitigate risk, manufacturers inspect bags before use which adds time and resources to the workflow. The overall cost of a bag leak depends on which step in the workflow (Figure 2).
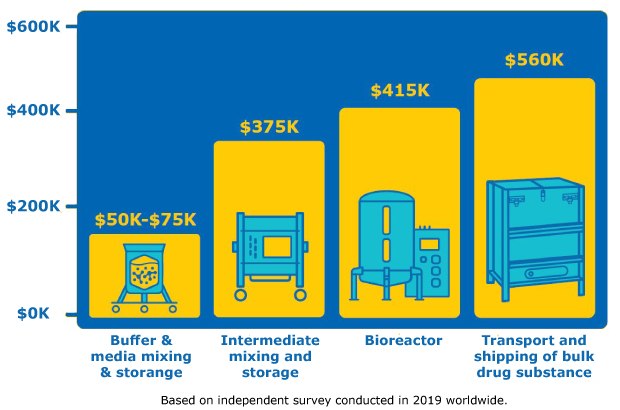
Figure 2:Average cost of single-use bag leak at different phases of bioprocessing; cost of leak in buffer mixing is much lower than cost of bioreactor bag leak or leak when transporting drug substance. Based on independent survey conducted in 2019 worldwide.
Bioprocessing Films For Mobius® Single-Use Assemblies
A single-use bioprocessing film should be chemically compatible with the processing fluid, compatibile with irradiation sterilization, and available in a format suitable for the processing volume or intended use. Our portfolio of single-use bags and containers offers options for every process and any processing volume including single-use bioreactors, Novaseptum® high purity sampling bags to larger volume 3D assemblies for single-use mixers.
Mobius® Essential assemblies are standard, off-the shelf bag and tubing assemblies, while our Mobius® assemblies are offered in both standard and configurable "fit for purpose" options, to meet the needs of every single-use application.
References
To continue reading please sign in or create an account.
Don't Have An Account?