Chemical Vapor Deposition
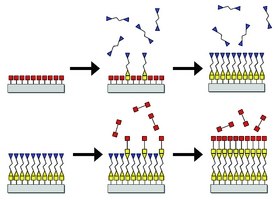
Chemical Vapor Deposition (CVD) is a method of epitaxially depositing films of solid materials on the surface of a substrate during the vapor phase of a controlled chemical reaction. CVD, also called thin-film deposition, is used prevalently for electronics, optoelectronics, catalysis, and energy applications, such as semiconductors, silicon wafer preparation, and printable solar cells.
The CVD technique is a versatile and quick method to support film growth, enabling the generation of pure coatings with uniform thickness and controlled porosity, even on complicated or contoured surfaces. In addition, large-area and selective CVD is possible on patterned substrates. CVD provides a scalable, controllable, and cost-effective growth method for the bottom-up synthesis of two-dimensional (2D) materials or thin films such as metals (e.g., silicon, tungsten), carbon (e.g., graphene, diamond), arsenides, carbides, nitrides, oxides, and transition metal dichalcogenides (TMDCs). To synthesize well-ordered thin films, high-purity metal precursors (organometallics, halides, alkyls, alkoxides, and ketonates) are required.
The composition and morphology of layers varies depending on the chosen precursors and substrate, temperature, chamber pressure, carrier gas flow rate, quantity and ratio of source materials, and source-substrate distance for the CVD process. Atomic layer deposition (ALD), a subclass of CVD, can provide further control of thin film deposition through sequential, self-limiting reactions of precursors on a substrate.
Featured Categories
Our high-quality solution deposition and vapor deposition precursors are optimal for...
We provide a broad spectrum of high-purity salts, both anhydrous and hydrated, ranging from 99.9% to 99.999% purity as measured by inductively coupled plasma mass spectrometry (ICP-MS) or inductively coupled plasma optical emission spectrometry (ICP-OES).
Related Articles
- atomic layer deposition (ALD), microelectronics, Mo:Al2O3 films, nanocomposite coating, photovoltaics, semiconductor devices, W:Al2O3 films, composite films, layer-by-layer
- Copper deposition processes are crucial for microelectronic interconnects in ALD development.
- Highly reducing or oxidizing species enhance organic semiconductor conductivity by reducing charge-carrier injection barriers.
- Catalytic water splitting produces hydrogen crucial for renewable energy, petroleum refining, and chemical industry applications like methanol production.
- Atomic layer deposition (ALD) showcases innovation in novel structure synthesis, area-selective deposition, low-temperature deposition, and more.
- See All (12)
Find More Articles and Protocols
How Can We Help
In case of any questions, please submit a customer support request
or talk to our customer service team:
Email custserv@sial.com
or call +1 (800) 244-1173
Additional Support
- Calculators & Apps
Web Toolbox - science research tools and resources for analytical chemistry, life science, chemical synthesis and materials science.
- Customer Support Request
Customer support including help with orders, products, accounts, and website technical issues.
- FAQ
Explore our Frequently Asked Questions for answers to commonly asked questions about our products and services.
To continue reading please sign in or create an account.
Don't Have An Account?