Glass vials and beakers are molded by mass production, but customized scientific glassware is handcrafted and repaired by highly-trained scientific glassblowers in a process filled with sparks, pops and tense moments.

Mike D'Acquisto II, a scientific glassblower, directs fire to the neck of a round-bottom flask.
February 24, 2023 | 5 min read
Flames hiss from torches, glass shards crash into waste bins and artists don face shields like they’re readying for a medieval battle. Some button-up shiny silver jackets, which, in addition to serving as a space-age fashion statement, include Kevlar fibers that withstand heat up to 1600 °C.
Merck's glass shop in Milwaukee, Wisconsin, USA, has all the elements of lively show. And by all accounts, it is.
A team of seven glassblowers design, create and repair custom scientific glassware in all shapes and sizes — from distillation columns over a meter tall to ones that easily fit into the palm of your hand. Scientists — most frequently chemists — leverage specialized glassware to control temperature and drip rate when synthesizing new molecules. In short, glassware helps keep labs in operation.
“Chemists tell us what they need and it’s the glassblower's job to make it a reality,” says Jason Noll, the glass shop manager.
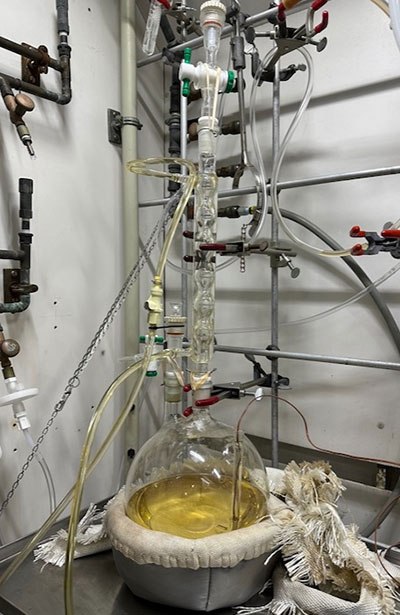
A round-bottom flask sits on a lab bench in Sheboygan, WI.
A few years back, chemists from Sheboygan, Wisconsin, asked the glass shop for a round-bottom flask the size of a yoga ball — a very common request for glassblowers as they make 50- and 72-liter flasks weekly. The piece made the perfect addition for the chemists to scale up their synthesis and the flask held its own amidst a deluge of tests from liquids, metal clamps and elaborate bench set-ups for years.
One day, while dismantling a distillation column, a chemist chipped the flask’s neck — an honest mistake and a somewhat regular occurrence. Not all breaks are created equal and this one meant that their work ground to a halt. The supply closet had no extras on hand. Sweating a bit, the lab group scrambled to come up with a replacement. While purchasing a new replacement would mean weeks of lost progress, the lab knew Merck’s glass shop could repair the flask much faster. The chemists shipped the piece off and asked the team to expedite the fix.
Upon arrival in the glass shop, Al Timmermann, the receiving clerk, carefully unpacks the flask and assesses the damage. Sorting from over 500 pieces, he selects the parts needed to make the repair. Mike D'Acquisto II, a seasoned glassblower, collects the tub of parts and heads to his workstation. He hoists the giant round-bottom flask into his lathe, fires up the heat and slowly warms the flask.
“If I jumped on that piece without warming it up, thermal shock would crack it, and that’s easily a $1,200 mistake,” he says.
After warming the flask, D'Acquisto returns to the workstation, drops his face shield and starts to work. With the flip of a switch, the flask begins to spin steadily on the lathe. Two flames start to roar, and he centers them near the flask’s neck. Even though there is just a small chip, he must remove the entire joint.
A large round-bottom flask spins on a lathe as D'Acquisto adjusts the intensity of heat using multiple fire sources.
This step requires patience. “Even when you think it’s time, it’s just not time,” he says. If you try to separate the neck from the bottom too soon, it can damage the entire piece.
Using a graphite rod, he re-shapes the neck of the flask, sizes it down to the diameter of the new socket joint requested by the chemists and slowly separates the two pieces. He smooths the opening left behind to ensure the glass’s thickness at the opening — or wall weight — remains the same throughout. Uneven wall weights create weak points in the glass and they are the nemesis of glassblowers.
D'Acquisto patiently waits for the glass to reach the correct temperature and then removes the damaged neck of the flask.
Grabbing the new neck for the round-bottom flask, he slowly heats it up and starts the process in reverse. A few minutes and a few more flames later, a new neck graces the top of the flask.
The act nears an end but one of the most stressful moments is yet to come. And it doesn’t involve any flames. D'Acquisto must move the piece before it starts to cool down or risks the entire flask shattering.
He sticks his gloved hands directly into the flames to heat them up and grabs hold of the flask. With a quick signal to his colleague, he shimmies across the shop while his colleague cranks open the door of the massive oven. D'Acquisto slides the flask in and quickly shuts the top. The piece will continue to strengthen in the oven overnight. The following day, Timmermann will carefully pack it up and ship it off to reunite with its excited lab family.
Soon, the round-bottom flask will resume its position on the lab bench and chemists will carry on their show. Before long, they’ll request another apparatus, repair or special custom job. And the glass shop will fire up and carry on their show.
About the glass shop
The glass shop in Milwaukee, Wisconsin, USA, serves as a center of excellence and innovation in the design and manufacture of glassware for chemists worldwide. They design and create a wide variety of glassware, including multiple jacketed condensers, silver jacketed columns and more.
To continue reading please sign in or create an account.
Don't Have An Account?