Additive Manufacturing of Permanent Magnets
M. P. Paranthaman1, I. C. Nlebedim2, F. Johnson3, S. K. McCall4
1Oak Ridge National Laboratory, Oak Ridge, TN 37831, USA, 2Ames Laboratory, Ames, IA 50011, USA, 3GE Global Research, Niskayuna, NY 12309, USA, 4Livermore National Laboratory, Livermore, CA 94550, USA
Material Matters, 2016, 11.4
Introduction
Permanent magnets are an essential technology for energy conversion. Motors and generators are used to convert energy between electrical and mechanical forms. Permanent magnets must be pre-charged (magnetized) prior to their use in an application and must maintain this magnetization during operation. In addition, permanent magnets must generate sufficient magnetic flux for a given application. Nevertheless, permanent magnets can be demagnetized by a number of circumstances, including the presence of other magnetic materials in their service,1 temperature changes (thermal demagnetization), microstructural degradation, and even the magnet’s own internal demagnetizing field. Therefore, the performance of a permanent magnet can be best understood by examining its ability to withstand demagnetization and to supply the magnetic flux required in a given application. Some of these properties are discussed further. Additive manufacturing, followed by exchange spring magnets will be discussed later.
Coercivity
Coercivity is the magnetic field required to reduce the magnetization of a material that is magnetized to saturation down to zero. It is a measure of the ability of a magnetic material to resist demagnetization, i.e., the permanency of a material’s magnetization. The term coercivity is often used interchangeably with coercive field, the term for any magnetic field that reduces magnetization to zero whether or not the material was previously magnetized to saturation.
Magnetic materials are classified as hard or soft based on coercivity. Hard magnetic materials such as permanent magnets have high coercivity, while soft magnetic materials such as electrical steel have low coercivity. Coercivity is a structure-sensitive extrinsic magnetic property, affected by temperature, crystal anisotropy, stress-state, and microstructural impurities.2 Controlling the properties that affect the structure of permanent magnets is pivotal to the progress that has been made in enhancing coercivity. In permanent magnets, B = μ0(H+M), two types of coercivity exist; the field at which the magnetic induction B is zero (Hc) and the field at which magnetization M is zero (intrinsic coercivity, (Hci)). The former is significantly less than the latter. Figure 1 shows that rareearth (RE) permanent magnet alloys based on Nd2Fe14B (NdFeB or Neo) and RE-Co have very high coercivity.3 Coercivity is often enhanced in Nd2Fe14B by the addition of dysprosium. There are commercially available sintered Nd2Fe14B magnets with a coercivity of ~3,000 kA/m (~38 kOe). Shorter specimens are more susceptible to internal demagnetization and, therefore, must have higher coercivity to match application specific requirements. AlNiCo magnets typically have low coercivity and, thus, must be made long and thin in order to minimize any demagnetization effect. One can select an optimized geometry by using the load lines and/ or permeance coefficients of permanent magnets, as shown in Figure 2.4
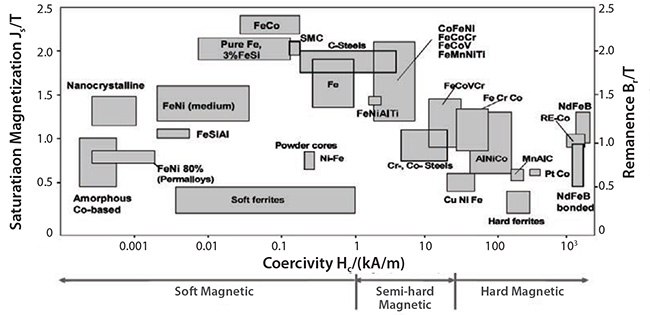
Figure 1.Coercivity, saturation magnetization, and remanence of various magnetic materials.
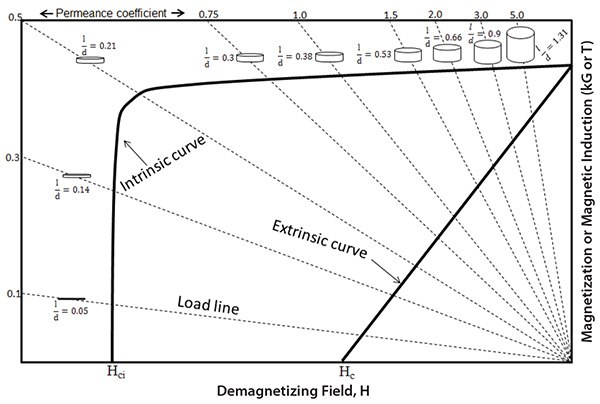
Figure 2.Demagnetization curve of a sintered Nd2 Fe14B magnet showing the permeance coefficient and corresponding sample geometries for each load line.
Remanence
Remanence is the residual magnetization that remains when no magnetic field is applied to a magnetic material that was previously magnetized to saturation. It is often used interchangeably with the term remanent magnetization, or the residual magnetization when no magnetic field is applied, whether or not the material was previously magnetized to saturation. Remanence is directly related to the amount of magnetic flux that can be generated with a permanent magnet. Figure 1 also shows the remanence values of different magnetic materials. Soft magnetic Fe– Co alloys have significantly higher remanence than permanent magnet materials. In permanent magnets, remanence values obtained with closed loop measurement systems will be higher than the open loop remanent magnetization since the effective field under closed loop configurations is identical with the applied field. This means that in applications that are normally open loop conditions, the remanent magnetization under which a permanent magnet operates will be less than its remanence value. In specimens with very low demagnetizing factors (e.g., toroid and long cylinders), the remanence in open loop configurations approaches that of closed loop configurations. However, as specimens become shorter and thicker, the opposite is true. This is important in selecting the geometry of permanent magnets for applications.
Maximum Energy Product
Maximum Energy Product The maximum energy product, BHmax, has gained wide acceptance as a property to qualify the performance of permanent magnets. It is the maximum value of the product BH obtained in the second quadrant of the demagnetization plot and represents the maximum energy a permanent magnet can generate outside the magnet,1 measured in MGOe (cgs) or kJ/m3 (S.I.). The significance of BHmax in designing permanent magnet machines can be appreciated considering that the energy produced by a magnet of fixed size in an air gap outside the magnet is proportional to the product BH. As a result, the volume of magnet required to generate a given magnetic field strength outside the magnet is minimized when the product of BH is at the maximum value.5 Therefore in spatially restricted applications where smaller magnets are required, permanent magnets with a higher BHmax value can be used to maximize performance. Considering BHmax alone may not be sufficient to select a material for an application because it does not reflect the demagnetizing effect imposed by the shape of the permanent magnet. In applications where spatial constraints require a shorter and thicker magnet, the magnet should be operated close to the maximum coercivity in order to minimize the effect of the demagnetizing field, even when it does not coincide with the point where the product BH is at the maximum. Ceramic magnets (ferrites) have low BHmax values but due to their higher coercivity may be preferred to AlNiCo magnets for such applications. Conversely, if a large magnetic flux is more important than resistance to demagnetization, long specimens of AlNiCo magnets are preferred to ceramic magnets in order to operate at the highest value of BH where the high remanence in AlNiCo can be utilized. In general, to maximize the energy generated from a permanent magnet in a given application, one needs to select a load line that maximizes the product BH while also meeting geometrical requirements. The room temperature demagnetization plot of a sintered Nd2Fe14B magnet in Figure 2 shows the permeance coefficient and the corresponding sample geometries for each load line. The operating point of the magnet is the intersection between the load line and the extrinsic magnetization curve.
Magnetic Anisotropy
Magnetic Anisotropy The term magnetic anisotropy refers to the directional dependence of magnetic properties. Magnetocrystalline anisotropy, significantly exploited in developing permanent magnets, is an intrinsic form of magnetic anisotropy. The consequence of magnetocrystalline anisotropy is that materials are easier to magnetize in certain crystallographic directions than in others. The energy that aligns the magnetic moments in the easy magnetization direction is the magnetocrystalline anisotropy energy. It arises from the coupling between the spin and orbital motions of electrons (spin-orbit coupling) and, therefore, may be considered as the energy required to overcome the spin-orbit coupling.6 It is often expressed in terms of the magnetocrystalline anisotropy constant, K1 (ignoring the higher order constants; K2, K3, …, which may be significant in certain conditions). If K1 is positive, there is an easy axis and a hard plane. If K1 is negative, there is a hard axis and an easy plane. Materials with low crystal symmetry typically have higher anisotropy constants than those with higher symmetry. For example the magnetocrystalline anisotropy in hexagonal cobalt is an order of magnitude higher than that in iron with a cubic crystal structure. The relatively high anisotropy of CoFe2O4 compared to other cubic materials is due to the contribution of the unquenched orbital angular momentum of Co to spin-orbit coupling.7 The contribution to the spin-orbit coupling that results in high magnetocrystalline anisotropy in rare-earth based permanent magnets comes from the rare-earth 4f electrons. The rotation of the magnetic moments in response to an applied magnetic field can be viewed as the competition between the magnetic energy and the magnetocrystalline anisotropy energy. The magnetic field strength required to rotate magnetic moments, inclined at an angle θ to the field direction, into the field direction is given in Equation 1. When the magnetic moments lie along the easy direction at 90 ° to the field direction, the magnetic field strength (H) needed to rotate magnetization into the field direction is the equivalent of the anisotropy field (HA) given in Equation 2. To attain saturation magnetization, magnetic field strength equal to or greater than the anisotropy field needs to be applied.
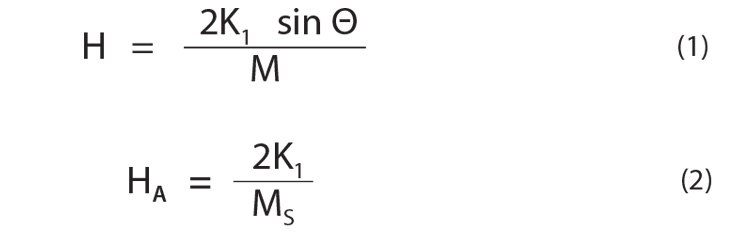
Equation 2 is important for developing permanent magnets and shows why high magnetocrystalline anisotropy is desirable. The anisotropy field is often considered the maximum attainable coercivity in permanent magnets for a material magnetized to saturation. Applying this to permanent magnet manufacturing requires that the easy magnetization directions in all the grains constituting a permanent magnet be aligned. Once aligned, a strong magnetic field is required to rotate them and, thus, they are not easily demagnetized. This helps to relate magnetocrystalline anisotropy (an intrinsic property) to coercivity (a measure of resistance to demagnetization) which is an extrinsic magnetic property. It also shows why magnetocrystalline anisotropy is one qualifying criteria for selecting materials in permanent magnet applications. So far, the discussion on anisotropy assumes that the magnet acts as a uniformly magnetized piece in which all magnetic moments rotate uniformly when a magnetic field is applied. In practice, there are regions of uniform magnetization called magnetic domains, separated by domain walls—regions in which magnetization gradually switches from the direction in a domain to that in an adjacent domain.8 There is, therefore, another energy that competes with the magnetocrystalline anisotropy energy called the exchange energy. Exchange energy tends to increase the thickness of the domain walls, whereas anisotropy energy tends to decrease it. In addition, microstructural imperfections that obstruct the propagation of magnetic domains also contribute to coercivity. In practice, measured coercivity is less than the anisotropy field demonstrating that coercivity in an extrinsic property which, apart from anisotropy, depends on other factors.9
Shape Anisotropy
Shape anisotropy can also be crucial in permanent magnet development and applications. Due to shape anisotropy, it is easier to magnetize a material along the longer axis in which the demagnetizing field is less, than along the shorter axis which has a stronger demagnetizing effect. Since an applied magnetic field must overcome the anisotropy field, in addition to rotating the magnetic moments, the effective field (Heff) is smaller than the applied field (Happ) by the magnitude of the demagnetizing field (Hd = NdM), as shown in Equation 3. The demagnetizing field depends on the geometry of the material (represented by the demagnetization factor, Nd) and the magnetization in the material.

In producing AlNiCo magnets, efforts are focused toward enhancing shape anisotropy because the coercivity in AlNiCo is derived mainly from that shape anisotropy. In permanent magnet machine designs, the effect of shape anisotropy is also accommodated by selecting the appropriate load lines.
Curie Temperature
Ferromagnets (and ferrimagnets) transition to a paramagnetic state above their Curie temperature: a structure-insensitive magnetic property of materials. Above the Curie temperature, thermal energy overcomes the interaction energy that keeps the magnetic moments aligned, resulting in disordered magnetic moments, a sudden drop in magnetic susceptibility, zero remanence, and zero coercivity. High Curie temperatures are, therefore, desirable in order to use permanent magnets at elevated temperatures. Since magnetic properties continuously degrade as specimen temperature approaches the Curie temperature, there is typically a temperature (below the Curie temperature) above which a permanent magnet will perform below its rating. This temperature is called the maximum operating temperature or maximum working temperature. Typical Nd2Fe14B magnets have Curie temperatures in the range 300–320 °C, but the maximum operating temperatures are often between 80–120 °C. Ultra-high grade Nd2Fe14B magnets have a maximum operating temperature of ~180 °C.
Two other parameters are also important for describing the temperature dependence of the properties of permanent magnets. The reversible temperature coefficient of residual magnetic induction (α) is the percentage change in magnetic induction with change in temperature. Similarly, the reversible temperature coefficient of coercivity (β) is the percentage change in coercivity with temperature change. Depending on the application, these parameters can play a key role in the choice of a permanent magnet material. For example, permanent magnets used in applications like gyroscopes and accelerometers should have as low an α value as possible.10
Apart from the properties discussed so far, there are other aspects that can influence the choice of one permanent magnet material over another in an application. One example is corrosion resistance. Sintered NdFeB magnets are known to be very susceptible to corrosion due to multiple microstructural phases and can corrode faster than iron.5 Hence, these materials are usually coated with nickel, zinc, and aluminum. In polymer-bonded magnets, the binder material provides protection from corrosion. One advantage of samarium cobalt magnets is that they are less susceptible to corrosion than NdFeB magnets. Nevertheless, NdFeB magnets have better tensile, bending, and compressive strengths. As a result, Sm–Co magnets are more prone to breakage than NdFeB magnets. Ferrites and AlNiCo-based magnets have much better corrosion resistance than the rare-earth based magnets, but ferrite magnets are more brittle than AlNiCo magnets.
Additive Manufacturing
During the last decade, the use of permanent magnets in green energy technologies has skyrocketed. Rare-earth based permanent magnets such as Nd2Fe14B (NdFeB) and SmCo5 are essential components in mass market products such as audio speakers, hard-disk drives, elevators, electric vehicles, wind turbines, and aerospace applications. However, the high cost of rare-earth magnets, supply and availability of rare-earth resources, and the technical issues associated with the reliability of clean technology devices needs to be resolved in the future. The high cost of permanent magnets is mainly a result of the uncertainties of rare-earth elements. Considering that most of the US rare-earth magnet manufacturing capability was transferred to Asia and Europe in the last decade,11 novel methods that avoid or minimize the use of rare-earth elements need to be developed to reduce US vulnerability to rare-earth price spikes. One of the main strategies of the Critical Materials Institute research is to develop a viable additive manufacturing technique for the fabrication of near-net shape magnets. Conventional manufacturing methods used to make permanent magnets are inefficient and generate a sizeable waste during cutting and slicing of magnets to the required shapes and sizes. Recovering and remanufacturing rare-earth elements from the waste material is also not an easy task considering that rare-earth elements tend to oxidize. Therefore, alternative methods are needed that not only require less energy during manufacturing but also generate less waste material. One way to minimize the waste generated during permanent magnet manufacturing, and to reduce its overall cost, is to use additive methods to fabricate complex geometries of magnets that minimize waste. The additive manufacturing approach has the additional advantage of enabling the fabrication of physical parts directly from the computeraided design (CAD) models, with no tooling required for fabricating magnets. In addition, the microstructure and properties of the magnets can be tailored using some additive manufacturing processes. Fabrication of magnets with metal additive manufacturing processes such as electron beam melting, laser additive manufacturing, electrophoretic deposition, and cold-spray deposition techniques are currently in development and testing, with results expected in the near future. Unlike conventional techniques, metal and polymer additive techniques make highly efficient use of energy and raw materials because materials are deposited only where they are needed. At the same time, additive manufacturing eliminates the need for specialized tools to make certain shapes and sizes.
Bonded NdFeB permanent magnets have grown into an important segment of the permanent magnet market with an estimated global market size of over $750 million. Bonded magnet manufacturing processes include: compaction (using thermoset polymers such as epoxy, acrylic, phenolic, etc. and a curing temperature of 150–175 °C); injection (using thermoplastic polymers such as nylon, polyphenylene sulfide (PPS), etc.); elastomers (using nitrile rubber, vinyl, etc.); and calendaring process.12–20 Two manufacturing methods are typically utilized to fabricate the majority of bonded Neo magnets including injection molding using a thermoplastic binder and compression bonding using a thermoset binder. The reported energy product for injection-molded bonded Neo magnets ranges between 5–11 MGOe. However, for compaction bonded Neo magnets, a relatively higher energy product of 8–17 MGOe has been achieved. Bonded NdFeB magnets have better corrosion resistance and better ductile properties compared to sintered NdFeB magnets. Recently, isotropic NdFeB-bonded magnets with complex shapes have been successfully printed using direct write methods,21 binderjet printing,22 and big area additive manufacturing23 techniques. The challenge in additive printing of anisotropic NdFeB magnets is increasing the magnet loading of >65 vol% while still maintaining anisotropy with perfect grain alignment in complex shapes and throughout the thickness of the magnet. Thus, innovative methods are still needed to produce NdFeBbonded magnets with high energy products.
Exploiting the Mesoscale with Exchange Spring Magnets (A New Type of Hybrid)
Nanocomposite exchange spring permanent magnets are one composition with the potential to exceed the performance of current state-of-the-art sintered rare-earth permanent magnets.24 The potential of exchange spring magnets comes from their remanent magnetization enhanced by a highly magnetized soft phase such as iron, while exhibiting high intrinsic coercivity at the same time. This high intrinsic coercivity is provided by a hard magnet phase with large, uniaxial magnetocrystalline anisotropy. Early work predicted energy products as high as 120 MGOe (1 MJ/m3).25 More recent numerical simulations have suggested that energy products of 85.2 MGOe (0.678 MJ/m3) may be more attainable.26 This value is still in excess of the maximum possible energy product of 64 MGOe (0.515 MJ/m3) exhibited by Nd2Fe14B sintered permanent magnets.27 Such a property improvement in nanocomposite magnets requires three conditions be met: (1) the saturation magnetization of the soft phase must exceed that of the hard phase; (2) the magnetically “easy” axes of the hard phase components must be aligned parallel to one another; and (3) the characteristic dimensions of the microstructure (for example, grain size) must be fine enough to allow the phases to be magnetically coupled by the ferromagnetic exchange interaction. Figure 3 is a schematic of the microstructure of a conceptual nanocomposite magnet.
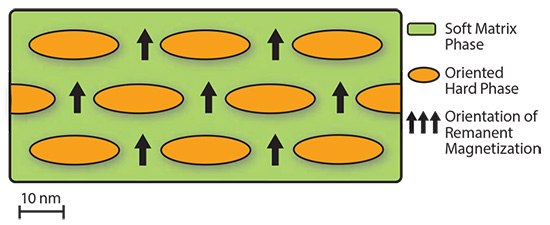
Figure 3.Schematic of nanocomposite magnet microstructure illustrating the key requirements of particle size and orientation.
To date, these three requirements have been fully met only in composites produced by thin and/or thick film processing methods.28–31 Isotropic nanocomposite magnets have been produced by rapidly solidifying Nd2Fe14B alloyed with an excess of Fe.32 Under certain rapid quenching and annealing conditions, these magnets may form a two-phase structure that contains nanometer-sized grains of α-Fe and Nd2Fe14B.33 The magnetic remanence (BR) is enhanced when compared to an isotropic magnet produced without excess Fe. However, this “top-down” processing method does not enable easy axis alignment of the Nd2Fe14B. Thus, the energy products of these magnets are lower than those manufactured by high temperature sintering of magnetically aligned powders. Isotropic nanocomposite magnets have been commercialized in bulk as polymerbonded magnets by Magnequench.
The development of bulk nanocomposite magnets also includes “bottom-up” processing methods in which hard and soft magnetic phases are first produced as discrete nanoparticles that are then aligned and consolidated into bulk shapes. This route requires selection and development of multiple processing methods. Particle processing methods have included chemical, electrochemical, mechanical, and plasma synthesis methods.34,35 Both magnetic and mechanical particle alignment methods have been explored. Consolidation methods have included conventional thermal sintering as well as shear-assisted methods such as uniaxial and triaxial compaction, extreme shear deformation methods, and specialized methods such as spark-plasma sintering and dynamic magnetic compaction.36,37
Among the many challenges facing the various bottom-up processing methods is the need to retain the nanometer-scale dimensions of the discrete nanoparticles during consolidation and alignment. The large driving force for minimization of surface energy due to thermally activated particle coarsening makes conventional high temperature sintering processes impractical. Large surface area-to-volume ratios combined with the use of reactive rare-earth compounds make the nanoparticle precursor compounds extremely air sensitive and necessitate the use of inert-atmosphere environments with strict oxygen control. The hard and soft magnetic phases used in nanocomposite permanent magnets may not be thermodynamically stable in combination, leading to a metastable structure. Computational methods enable the prediction of magnetization curves and reversal fields for idealized nanocomposite microstructures.38–41 Both hard phase particles embedded in a soft phase matrix and hard phase particles embedded in a soft phase matrix have been numerically simulated. The calculations have progressed to the point where preferred microstructural dimensions can be specified for composite structures with regular structures and connectivity patterns. Additionally, progress has been made in understanding the dependence of coercivity on soft phase content. Further work must be performed to simulate irregular microstructures that are produced in practice, as well as to better understand the influence of temperature on composite magnetic properties. Experimental42 and computational43 work has also explored the fundamental nature of the magnetic coupling that exists at the interface between the hard and soft phases in nanocomposite magnets. Less work has been performed in bulk nanocomposite magnets. It is likely that advanced three-dimensional atom probe methods would be wellsuited to characterization of the fine structure of nanocomposite magnets. Substantial progress has been made over the past 25 years toward achieving the goal of higher energy product nanocomposite permanent magnets. This progress has been paced by concurrent advances in materials processing, characterization, and simulation technology. The need for high efficiency, environmentally sustainable electric power and transportation systems remains a key priority. This need justifies continued investment in novel permanent magnet materials.
Acknowledgment
This work was supported by the Critical Materials Institute, an Energy Innovation Hub funded by the U.S. Department of Energy, Office of Energy Efficiency and Renewable Energy, Advanced Manufacturing Office. Work at Ames Laboratory, operated by Iowa State University, was performed under Contract No. DE-AC02-07CH11358. Partially prepared by LLNL under Contract DE-AC52-07NA27344.
Notice: This manuscript has been authored by UT-Battelle, LLC under Contract No. DE-AC05-00OR22725 with the U.S. Department of Energy. The United States Government retains and the publisher, by accepting the article for publication, acknowledges that the United States Government retains a non-exclusive, paid-up, irrevocable, world-wide license to publish or reproduce the published form of this manuscript, or allow others to do so, for United States Government purposes. The Department of Energy will provide public access to these results of federally sponsored research in accordance with the DOE Public Access Plan (http://energy.gov/ downloads/doe-public-access-plan).
To continue reading please sign in or create an account.
Don't Have An Account?